High-quality metrology for quality control in the measuring room, production, incoming goods and development.
Gear Metering Pumps & Meter Mix Dispense Machines with highest accuracy for processing liquids and pastes.
High-precision rotary stroke bearings for backlash-free linear and rotational movements for use in machine and device construction.
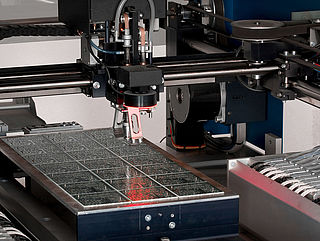
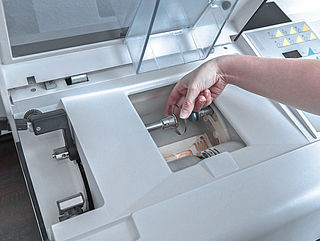
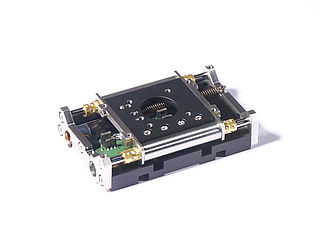
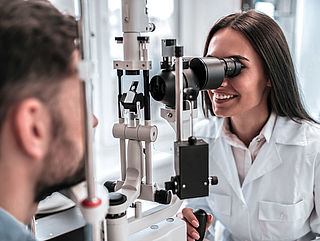
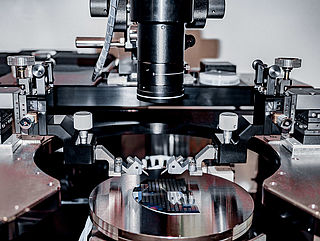
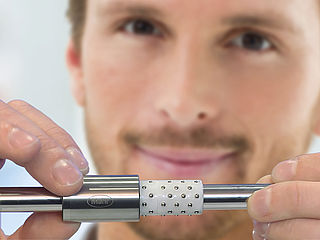
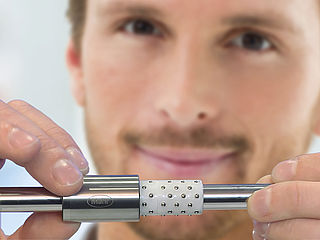
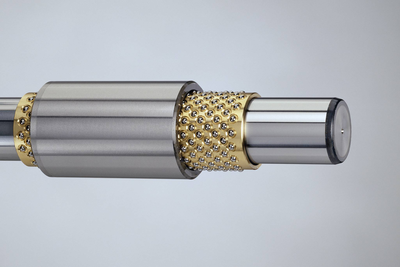
Ball-bearing guides for linear and rotational movements without play for use in all technical areas where reliability and precision are required.
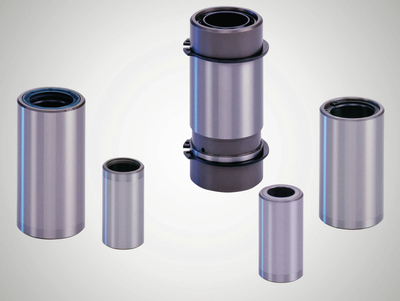
The guide diameter finely honed to ISO tolerance IT 3 guarantees the preload of the ball bearing guide in combination with shaft diameter ISO-h3.
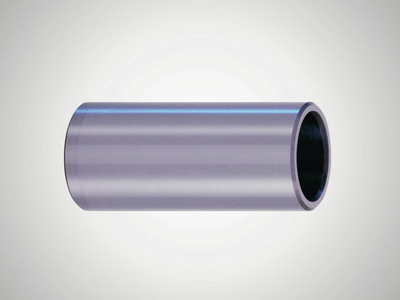
Universal, slim inner bevels on both sides.
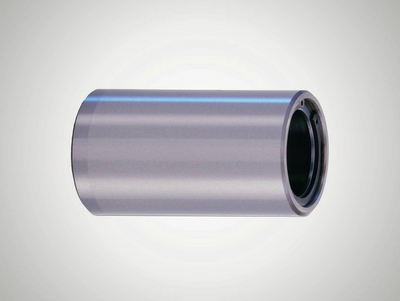
Permanently installed thrust washers on both sides provide a safe travel limit for the ball cage.
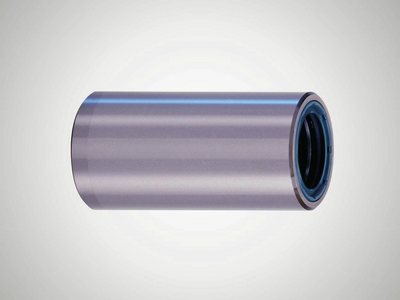
Permanently installed thrust washers on each side and sealing rings prevent impurities from getting into the ball bearing guide.
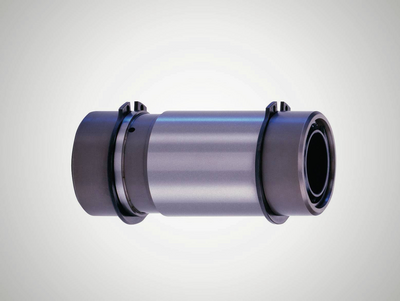
Extra sturdy model with scrapers on both sides which reliably prevent impurities from getting in, even in very dirty environments.
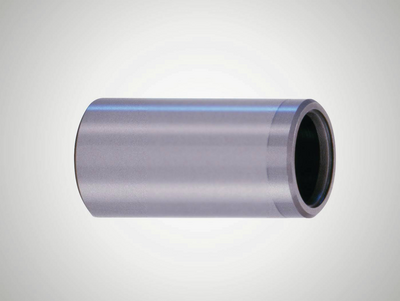
Universal, slim inner bevels on both sides, for use with ball cage from mini series N502.
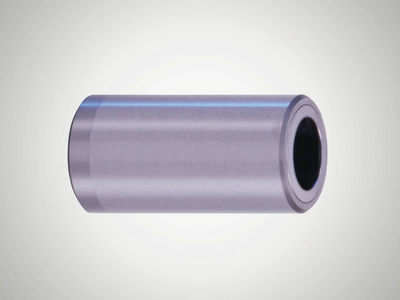
Permanently installed thrust washers on both sides provide a safe travel limit for the ball cage from mini series N502.
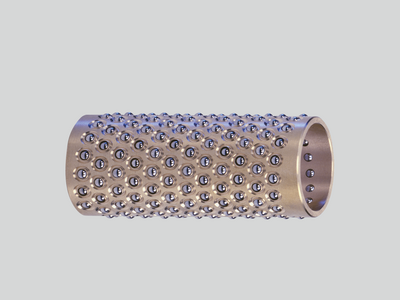
The balls can move easily without getting lost. The balls are arranged in such a way that they run smoothly and ensure a long service life of the ball bearing guide.
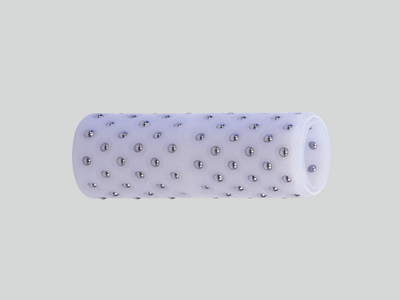
Excellent dry run properties and maximum smoothness, even at high accelerations thanks to the lightweight plastic.
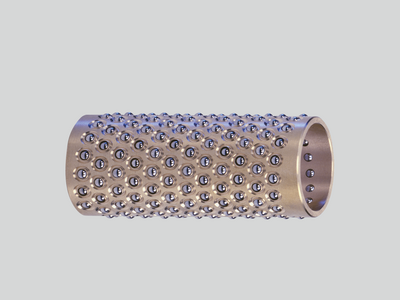
Versatile with balls arranged along a helical line, ideal for linear movements and rotational movements.
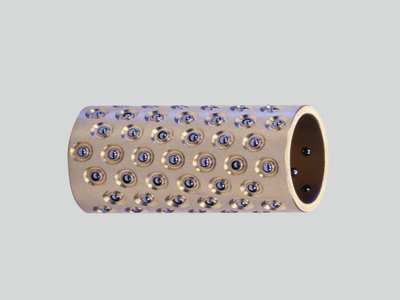
Smaller balls used with same shaft diameter compared to type N501. Reduced installation space thanks to guide bushes from the mini series.
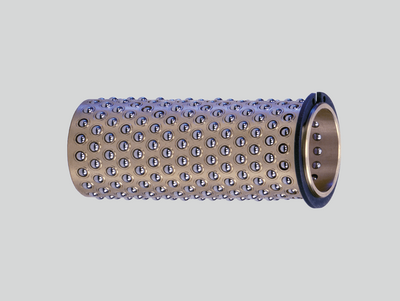
High loading capacity thanks to large number of balls, reliable travel limit for the cage thanks to the securing ring.
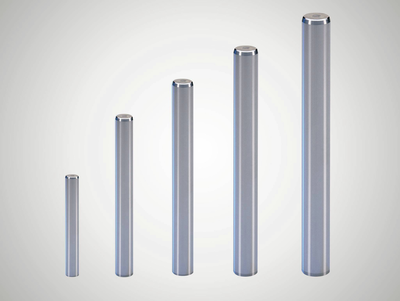
The finely-ground surface is ideal for high precision ball bearing guides, ensuring smooth running and a long service life of the ball bearing guide.
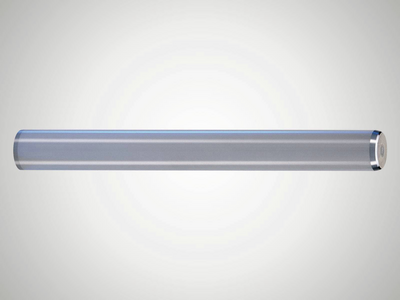
Preload is guaranteed when using with Mahr guide bushes and ball cages.
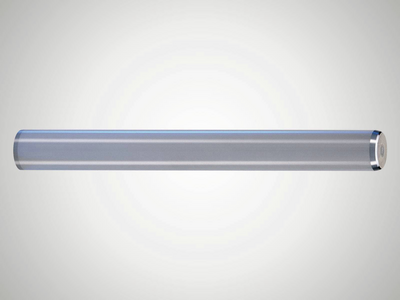
Inner thread on both sides, preload is guaranteed when using with Mahr guide bushes and ball cages.
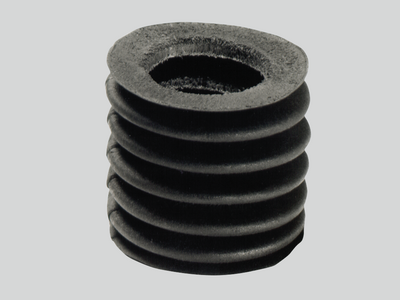
Broader and more optimized range of uses.
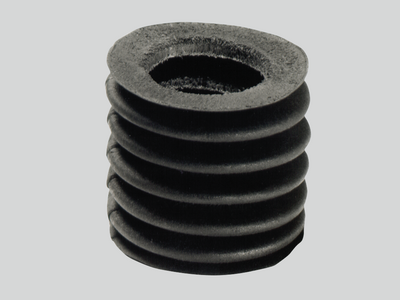
Protect open ball-bearing guides against dirt without compromising smooth movement.
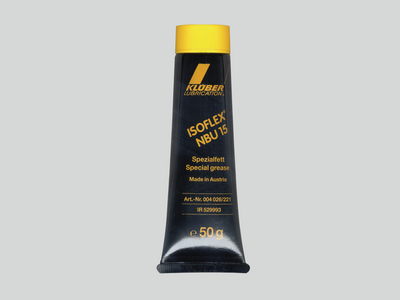
Lubrication for maximum performance and corrosion prevention.
Fixing the guide shaft
Other than the guide bush, the guide shaft can be clamped or installed with interference fit.
A radially loaded rotary stroke bearing will be affected by elastic deformations at the rolling surfaces and also on the guide shaft. The rigidity of the guide shaft is essentially determinded by the fixing used.
With a relatively high load, long shaft length and the requirement for high guide accuracy over the entire stroke path, at least at one end the clamping length should be designed with a length s ≥ 1.5 · dw .
In case of one-sided clamping (cantilever beam), apply the load as close to the clamping side as possible.
Interference fit
Produce a mounting bore, e.g. ISO-R6, with an accurately aligned axis position. The deviation of the parallelism of two paired shafts should not be greater than the amount of preload.
Clamps in mounting bore e.g. ISO-H6
- Indirectly using a slotted and draw screw.
- Directly using a pressure screw. For this purpose, flatten the shaft end slightly, drill or screw in to secure in the longitudinal direction.
Clamping in the V-block
- Using a clamp
- Using a draw screw
Bonding
The mounting bores for the shaft can be manufactured with a fitting tolerance, e.g. ISO F7-G7, to prevent distortions of the shaft and ball-bearing guide in the event of badly aligned mounting bores. Glue the shaft in the final assembly together with the ball-bearing guide and leave to cure in an aligned position. The instructions provided by the adhesive manufacturer regarding the adhesive gap, curing time, etc. must be observed.